Greetings, dear community!
Today, exactly a year, as I wrote the first post on Habré. The second and up to this point extreme post, I wrote about a week later and ...
This year I was actively engaged in the development of a new profession - Trouble-Shooter. Those who do not know such a specialty (but would like to know), you are welcome to my profile. In short, Trouble-Shooter is a person solving other people's business problems, not in traditional ways.
')
So, in honor of the anniversary of my presence at Habré, I decided to write a series of articles in which I will talk about some of the projects and developments made during the work on these projects. Of course, I will only talk about developments that the customer, for one reason or another, did not accept (respectively, all intellectual property rights belong to me) or which I did outside of projects for myself. And of course, all projects will be of a technical nature, this is about 40% of all projects (the rest are in the field of marketing, HR, economics).
It did not take long to start thinking about which project, it was logical to start from the very first project. Moreover, the solution that I will describe turned out to be really effective and simple (Trable shooters often have so simple solutions that the customer clutches his head: “How could I not have guessed it?”). There is no deception in the topic of the post, the really developed equipment turned out to be at least 20 times cheaper than its counterparts (for some brands of competitors, this figure reaches 40x), 2.5 times more accurate and much more convenient.
And so, as you already understood, we developed in this project not software, not processes, but equipment (hardware). Under the cut you will learn all the details about the project.
Customer: Large regional organization engaged in the wholesale of household chemicals and household goods for the home. More than 10,000 product items in stock.
Problem: In order to automate some logistic processes, it is necessary to have characteristics of its dimensions in the product database. For example, when calculating the load of machines, it automatically considers how much product will fit and how much and what kind of machines you need.
At the time of the appeal, these characteristics were entered manually into the database, however, measurements were also made manually (by a ruler). This led to inaccuracies that sometimes resulted in big problems.
Task: Develop a system for automatic and accurate measurement of the overall dimensions of goods of any shape (with rectangular boxes, everything is much simpler).
Primary analysis: A simple Google search showed that there are special measuring systems on the market that fully meet customer requirements in terms of technical characteristics.
The most popular brand, CubiScan, offered several models, but all of them are based on one principle: put the measured object on a transparent table, then move the frame with the integrated IR LEDs on 2 sides and the built-in IR receivers from opposite sides along the table. The controller counts the number of blocked beams horizontally and vertically multiplies by the distance between the LEDs and gets the size of the 2m axes. On the 3rd axis, the size is obtained by tracking the movement of the frame. The frame, depending on the model, can move in a straight line or along a circle (forming a 90 degree sector).



The only parameter which did not suit the customer is the price. Indeed, prices for foreign devices started at $ 30,000, and the most expensive Japanese device was $ 62,000. A little later, the Russian analogue of the Sensotek company appeared at a price of more than 1 million rubles.
Specified task: Develop a system for technical characteristics not inferior to foreign counterparts, costing no more than 100 thousand rubles.
Analysis:Inventing a bicycle is not a very rewarding task, so the first thing I tried to do was calculate the cost of production of an analogue of Kubiskan. The most expensive and inaccessible thing, in this device was the IR LED line, despite the simplicity of the product, its development poured into quite decent money and the cost of producing single products also did not allow significantly reduce the cost of construction.
The second step was the development of several alternative measurement methods (including using Kinekt, a 3D scanner, 2 video cameras, physical probes, etc.). I will not dwell on these methods, I will only say that they were abandoned because of the cost of development.
Conclusion: it is necessary to return to the first variant (analogue of Kubiscan) and make it very cheap.
Development:To reduce the cost of Kubiskan, it was necessary to solve 3 subtasks:
- Reduce the cost of IC line and its development.
- Cheaper weight measurement system. The fact is that the scales are built in Kubiskan and it is very convenient and although there was no such requirement in the customer’s task, I decided that you shouldn’t refuse such convenience, but it is worthwhile to work with its cheaper implementation.
- Develop a simple system for calculating the 3rd coordinate.
Reduce the cost of IR rulerTo reduce the cost of some part of the technical system, I always start by searching for commercially available analogues (or not quite analogs, but some device that can replace the original one). It is clear that the mass product will cost much less.
Search for analogues at a reasonable price, was not successful. Something similar is used to measure the geometry of wood, for example, but these are also expensive systems.
Helped his majesty the case. Having spent a tremendous amount of time and effort on finding a solution, I decided to switch to another project, get some rest, in the hope that it would help to look at the task in a new way. The new project included a touch screen. Starting to learn sensory technology, I learned about the existence of an infrared frame for touch screens. The principle of their operation is 1 to 1 as with a measuring IR ruler, only they determine not the size, but the coordinates.
Having contacted the Russian dealers of one of the Chinese brands, I found out that their SDK allows to get the area values of the object that blocked the rays. That was what I needed! In addition, this frame had a higher resolution (2 mm), an affordable price and the manufacturer could produce frames according to the size of the customer.
Subtask number 1 was solved - we measure the sensor infrared frame.
Cheaper weight measurement systemIn Kubiskan and its analogs, scales are a glass plate with sensors in the corners. This is quite a difficult decision, because sensor readings need to be synchronized and processed, and the sensors themselves with the required parameters are more expensive than ready-made trading scales. Therefore, the decision was such that you need to use ready-made scales. But they are not transparent.
Those who are familiar with TRIZ know that in such situations, when there is a contradiction and the whole power of this instrument is manifested. Without going into details, I will say that the solution was simple (like many solutions created by TRIZ) - we will move the frame not horizontally, but vertically, i.e. it will move from top to bottom and back.
So subtask number 2 was solved - we will use the existing trading scales (the choice fell on the built-in scales SHTRIH-Slim), while the measuring frame will move vertically.
Develop a simple system for calculating the 3rd coordinateIn Kubiskan, some distance measurement sensor is apparently used to measure the 3rd coordinate. Those. while the frame is moving, the sensor with some frequency scans the distance from some selected zero to the current frame position, at the same time the measurement of 2 coordinates by the frame itself takes place and at the end of the measurement a certain set of section areas is obtained, and information about the distance between these sections.
It seemed to me that this is not a reliable and method. Since for accurate measurement, it is required to train the operator to move the frame at a speed not exceeding a certain value. And the vertical movement made its own adjustments (if the operator releases the frame at the top point, then it will fall, that is, you need to think through some kind of shock absorbers).
Initially, I thought about moving the frame using a stepper motor. In this case, everything moves easily and measurements at all coordinates are easily synchronized. But the cost of ballscrews, guide rails, etc. components stopped me.
Next were the development of a lever system, a system with the use of gas lifts, etc. All this is not that. It is necessary to solve the issue with a stepper motor. Those. the stepper motor should be, and the ball screw should be in the system should not.
A long search led to the Openbuilds project. This is an open project, where the guys are developing linear motion modules based on aluminum structural profiles and belt drives.
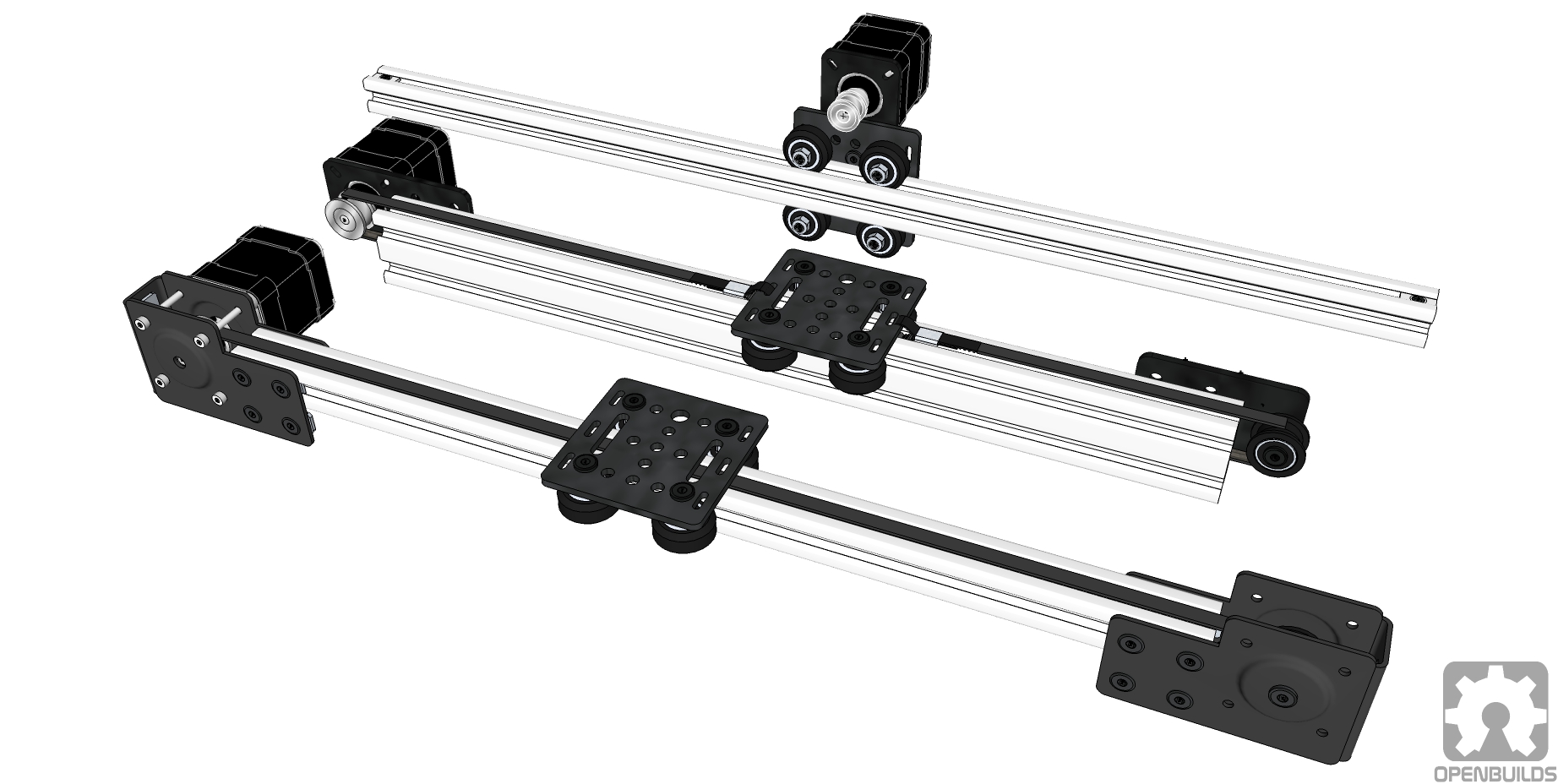
This solution made it possible to combine the device frame and guides for moving the frame. With even cheaper end device.
"Brain"Using a stepper motor instead of a manual drive has made some adjustments to the system. It was originally planned to build a USB splitter into the system and thus connect the scales and infrared frame to the PC with one cable (both the scales and the frame have a USB interface) and install the data processing software on the PC.
But now it took to control the stepper motor, and instead of another USB device (controller type Arduin), it was decided to implement the device Raspberry. Write software for it and connect the device to Ethernet, which allows (when writing a plug-in) to send measurement data directly to the central database of the 1C system. Also, you can directly connect any barcode reader to the raspberry (even USB, even RS-232).
TOTALAs a result, the development of such a device:
- A supporting frame made of a structural profile (from a factory assembly) is easily assembled (almost like “Lego”);
- IR touch frame in the casing of the U-shaped aluminum profile;
- Stepping motor and linear motion system Openbuilds;
- Built-in scales Stroke Slim;
- Built-in Raspberry as a system controller;
- Built-in LCD display;
- The only button to control the system ("Start measurement").
- The cost price of the device is about 50-60 thousand rubles, it is indeed 20 times cheaper than the cheapest analog and almost 60 times cheaper than the Japanese monster.
- Measurement accuracy - 2 mm, against 5 mm at analogs.
- Stepper motor, instead of a manual drive.
- Scalability - you can easily make a system for measuring a car or a person (for example, automatic measurement in a studio), because IR frames are available in a large assortment of sizes.
Unfortunately, the customer stopped the project at the stage of drawing up the TOR for programmers, not wanting to invest in development. Therefore, even the prototype was not published.
If one of the readers turns on to bring the idea to life, I will only be glad. You can ask questions.
If you make a working sample, please share the result.
PS In the following articles I will tell:
- about the development of a 3D printer for "printing" with any metals and alloys, with a resolution of about 20 microns, a speed of "printing" of about 10,000 cc. per hour and the uniquely low cost of the final product (the desktopmetal cries silently on the sidelines).
- about the Turk in which the coffee does not run away and in which there is not a single sensor (the “timecup” joined the “desktopmetal”).
- about the system that will force doctors and cooks to disinfect hands.
- and more about several developments.
Subscribe not to miss!
And maybe in vain I started this marathon? Write your opinion in the comments, is it worth it to continue?